Just about two and a half years ago I saw my first sample of COB tape light and I bet my jaw literally dropped. Tape light- a generic name for flexible linear LED strips- is a key tool in our quest for good lighting. We use it just about everywhere, and that makes us a little fanatic about the gear we choose.
The most common use of tape light is underneath upper kitchen cabinets for countertop illumination, but we also use it under vanities, under bar tops, in coves, behind mirrors, under beds, in shelving, in toe kicks, in closets, under steps, in handrails, under eaves, behind televisions, in lines on the ceiling, on top of timber beams and trusses, in slots, in skylights…you get the idea. I even experimented on my mom’s kitchen to demonstrate that we could do 100% of the lighting with tape.
Until COB tape, one key metric of tape light quality was pitch, or spacing between diodes. The tighter the pitch, the closer the diodes, the less “dotty” the appearance, the more even the illumination. And even illumination is the primary reason to use tape light, so I wanted my diodes as close together as possible.
In the early years of tape light, diodes could be spaced inches apart – I still see tape light occasionally with 2″ spacing. This is a bit like Christmas lights, nice for twinkle but awful in close quarters for even illumination. As quality and manufacturing abilities improved, smaller LED chips came to the market and pitch improved. The smaller gaps between diodes meant I could place LED strips even closer to surfaces, in tighter spaces, without worrying about dotting.
And then COB changed everything. Without changing the technology, really.
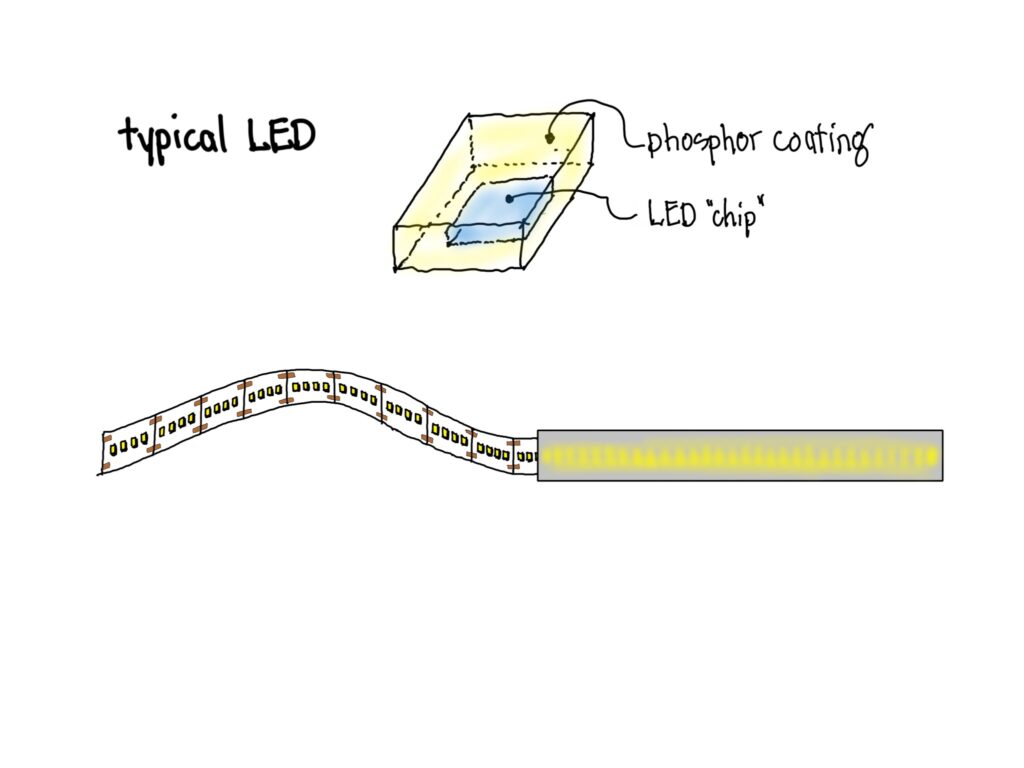
Standard LEDs have a diode (the “D” in LED), essentially a superconductor that creates light. Most often the color of light produced is not a nice white light (most are blue or red), so a layer of phosphors is placed on top the diode. The ugly color of light hits the phosphors, which then emit the desired color of light. It’s a two-step process not unlike fluorescent bulbs, which have a blue arc of light inside that is then converted to white light by a powdery coating of phosphors inside the glass.
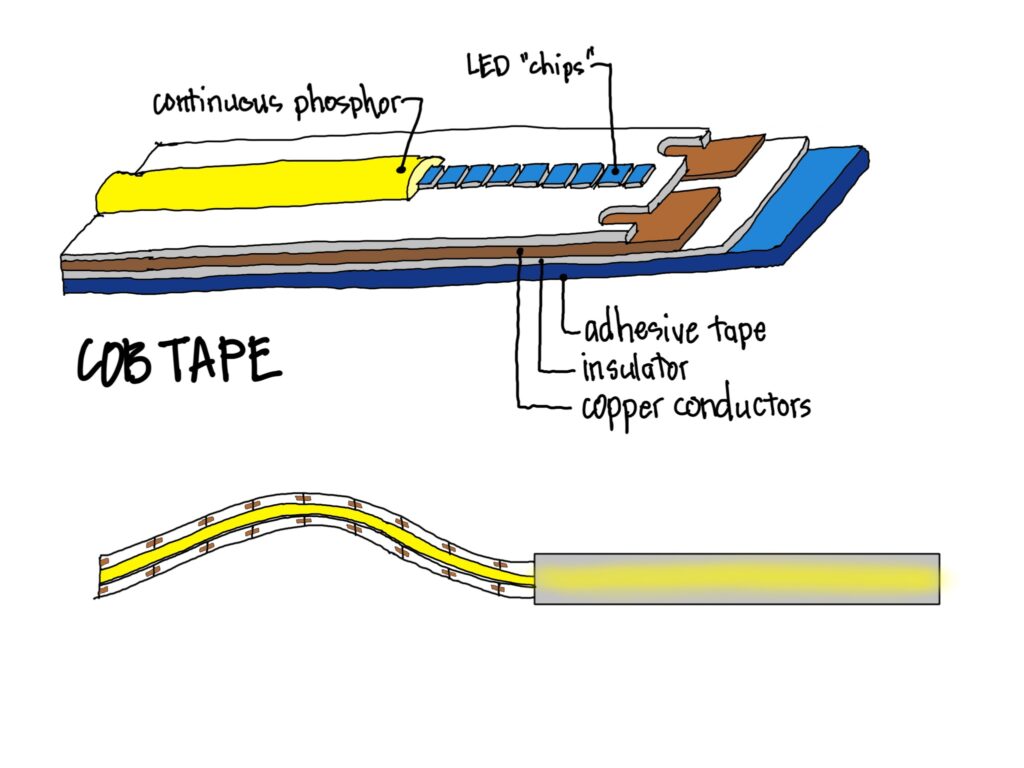
The geniuses behind lighting technology figured out that the diodes could be placed very, very close together, which made light almost continuous. Then someone – I don’t know who – figured out that the phosphor layer could be made continuous over the diodes and – voila- continuous light would be emitted. This is often called COB (chip-on-board) tape light, and it’s pretty dang cool.
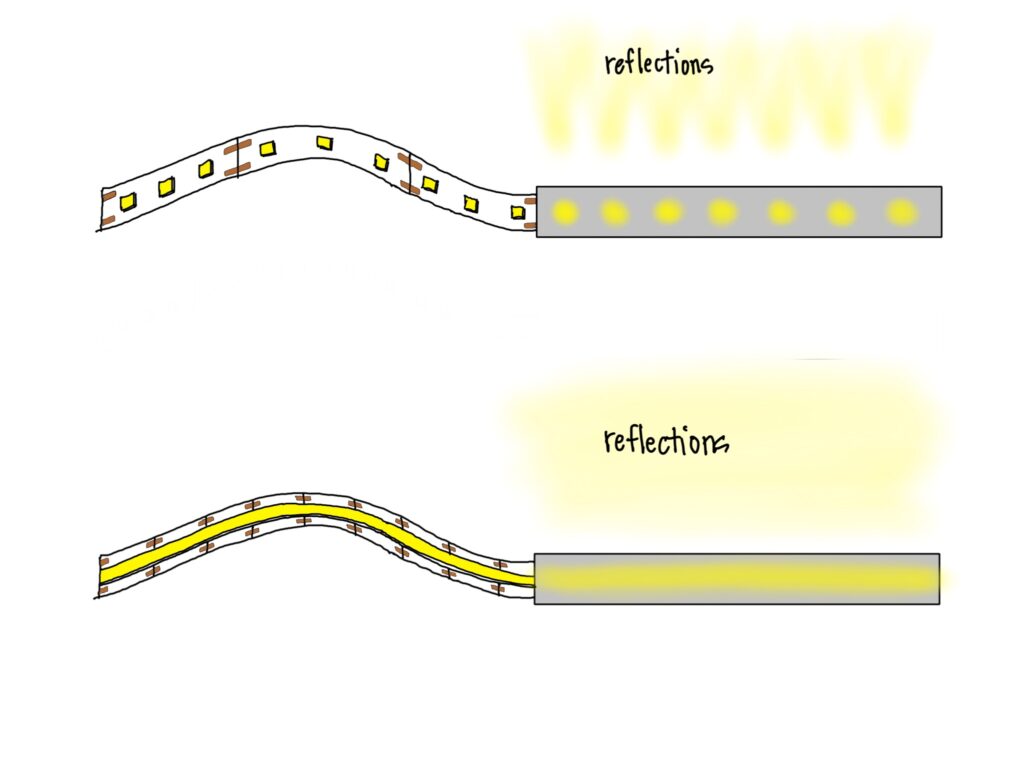
I personally hope that most tape light moves in this direction in the future, simply because it makes my job easier. I don’t have to worry as much about dotting when there are no dots seen. Yes, if you dim COB tape down it is often possible to see the tiny individual LEDs underneath the continuous layer, but under a lens or in a cove this will never be visible, even close-up. That means I can illuminate features with even less space, hiding LED tape in places it could not safely go before. And as a designer, it means I can do more with light.
So I’m not ashamed that I geek out about this stuff. COB tape is the kind of gear that makes my job fun.